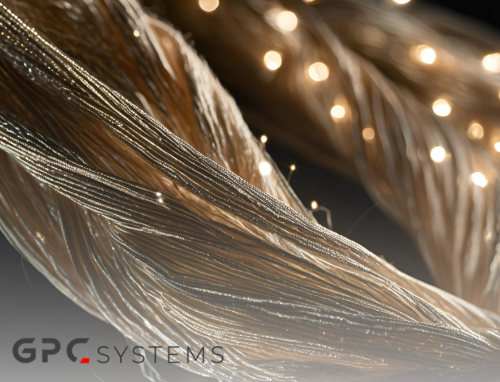
Transforming Workwear: The Future of Charging Stations in Clothing with Innovative Conductive Silk Thread
Researchers at Chalmers University of Technology in Sweden have developed an innovative silk thread coated with a conductive plastic material that could transform the textile industry by turning clothing into charging stations. This advancement has the potential to create wearable technology capable of powering electronic devices and sensors without relying on traditional batteries.
Key Features of the Conductive Silk Thread
The newly developed thread offers several advantages:
- Electrical conductivity: The thread can convert temperature differences into electrical potential, making it suitable for powering small electronic devices.
- Safety and flexibility: The materials used are non-toxic, bendable, and lightweight, meeting the high demands for wearable technology.
- Stability: The thread maintains its performance for at least a year and is machine washable, retaining two-thirds of its conducting properties after seven washes.
- Eco-friendly: The thread is made using only organic polymers, eliminating the need for rare earth metals commonly used in electronics.
Potential Applications in Various Workforces
This technology could significantly benefit workers in different industries:
Logistics
- Warehouse workers could wear clothing with integrated sensors to monitor their movements and prevent injuries.
- Delivery drivers could use their uniforms to charge mobile devices for navigation and communication.
- Inventory management could be enhanced with wearable scanners powered by the thermoelectric textiles.
Construction
- Safety gear could be equipped with health monitoring sensors powered by body heat.
- Workers could charge their communication devices on-site without relying on external power sources.
- Smart helmets with integrated lighting systems could be powered by the temperature difference between the head and the environment.
Current Limitations and Future Prospects
While promising, the technology still faces some challenges:
- Production efficiency: The current manufacturing process is time-consuming and requires manual labour.
- Power output: The demonstrated fabric produced about 6 millivolts at a 30°C temperature difference, which would require voltage conversion for practical applications.
However, the researchers are optimistic about the potential for developing an automated production process and scaling up the technology. As this innovation progresses, it could lead to significant advancements in wearable technology across various industries, improving worker safety, efficiency, and connectivity.
Join us here at GPC weekly for the latest news on tech, 3D, AI and much more.